
However, it should be noted that the effect of Zanchor process on mode II fracture toughness will depend on the material compositions, similar to the trend in mode I results. A quantitative study of the results indicates that the fracture toughness, G IIC, of the Zanchor composite, Z4, reached more than four times of the base composite, Z0.
LOW SPEC EXPERIENCE CRACK CRACK
On the other hand, the fracture toughness, G IIC, was approximately independent of the crack extension, Δ a, regardless of the Zanchor density, Z. All of the plots are the average values for three specimens.Īs shown in Figure 9.23, the fracture toughness, G IIC, increased largely and almost linearly with increasing the Zanchor density, Z, regardless of the crack extension, Δ a, except for the initial values for Δ a = 0 mm. The solid, shaded, and open circles represent the results for Δ a = 10, 20, and 40 mm, respectively. The open triangles represent the initial values for Δ a = 0 mm. The ordinate represents the mode II fracture toughness, G IIC. The abscissa represents the Zanchor density, Z.
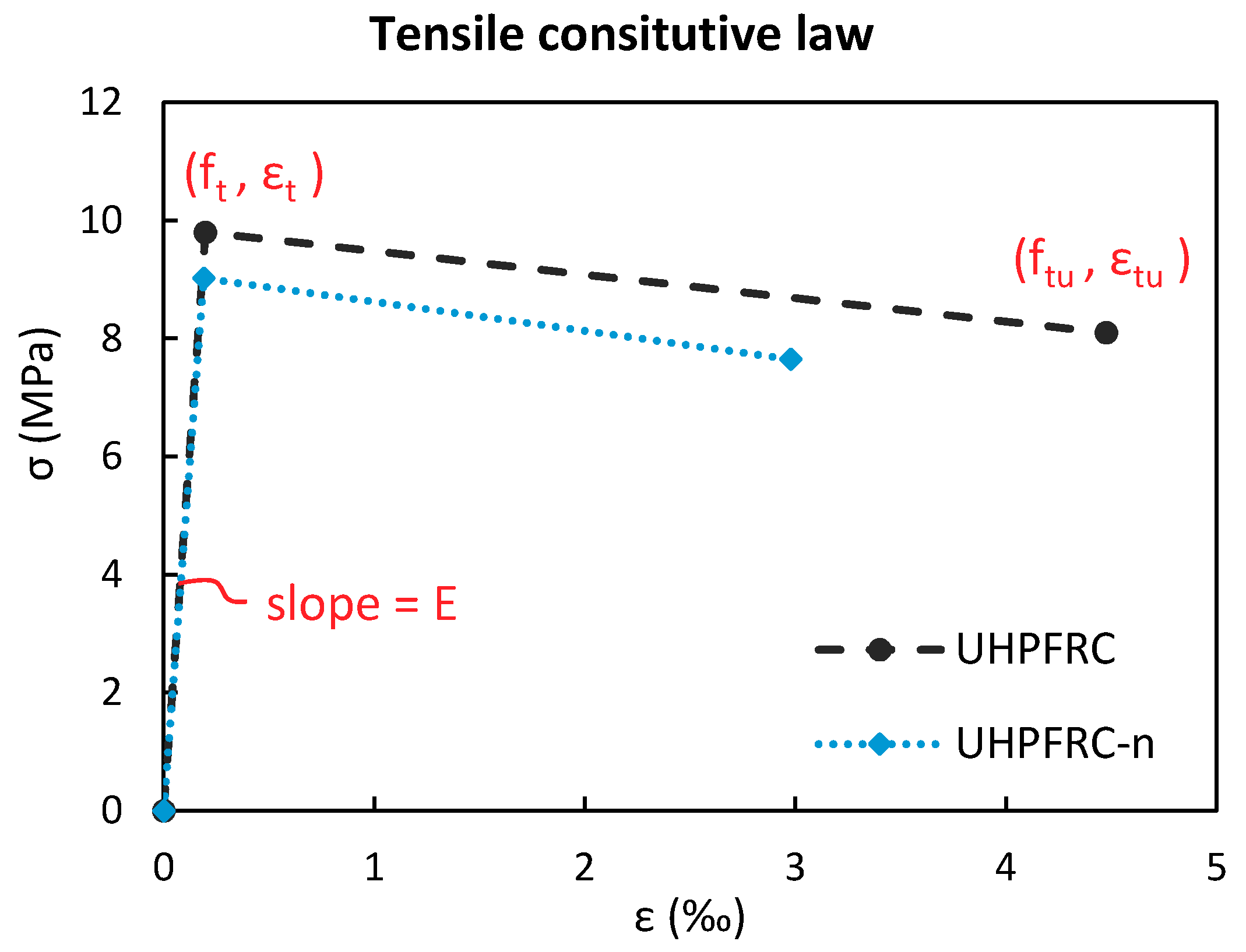
The ENF test results are summarized in Figure 9.23, parameterizing with the crack extension, Δ a. Relationship between Zanchor density and mode II fracture toughness. Such a silica layer with accompanying cracks is shown in Figure 22 after a 15,144 h field test with 92 starts ( Kimmel et al., 2003).įigure 9.23. They reported that after long-term exposures, a thick silica scale formed due to oxygen diffusion through the microcracks in the topcoat. (2007) have reported results of field tests of these EBCs. This is related to softening of the celsian phase at temperatures above 1200 ☌ leading to creep that heals the cracks. Cojocaru, Lévesque, Moreau, and Lima (2013) have reported significant crack-healing characteristics of the BSAS topcoat, with the density of vertical cracks reducing dramatically on cycling the coating at 1300 ☌ ( Figure 21). The reduction of cracking in the Si/(mullite+BSAS)/BSAS system was attributed to the reduction of stresses due to the lower elastic modulus compared to mullite. (2003) concluded that the Si/(mullite+BSAS)/BSAS EBC ( Figure 20(b)) was more robust than the Si/mullite/BSAS system due to its superior crack resistance, although the former is much more susceptible to formation of glassy phases, especially at higher temperatures. After exposure to 1400 ☌, the hexagonal phase almost completely converted to the monoclinic phase after 24 h. In the as-deposited samples, the BSAS phase was mainly a mixture of hexagonal celsian and amorphous phases, with the amorphous phase quickly converting to hexagonal phase at temperatures above 1200 ☌. Lee, Eldridge, and Robinson (2005) reported that BSAS exists in two polymorphs, monoclinic celsian, which has a close CTE match with SiC ( Table 1), and hexagonal celsian with a CTE that is about twice that of the monoclinic phase. This degradation was much more severe at temperatures above 1400 ☌. However, some areas in the mullite/BSAS and Si interface showed the formation of glassy reaction products. The coating system exhibited excellent protection of the substrate in water vapor-containing atmospheres at 1300 ☌.
LOW SPEC EXPERIENCE CRACK PLUS
Oxidation of the Si layer to form silica at the Si/(mullite+BSAS) interface of an EBC after a 15,144 h field test with 92 starts ( Kimmel et al., 2003).Īnother variant of these multilayered EBCs included an Si bond-coat, a mullite plus BSAS intermediate coat, and a BSAS topcoat, as seen in Figure 20(b) ( Lee et al., 2003). Evidently, the formation of an extensive diffusion zone between the mullite and the BSAS ( Figure 20(a)) did not appear to affect the durability of the coating system adversely.įigure 22. This Si layer improved the bond strength between the SiC and mullite, and these coatings exhibited excellent protection of the substrate after a 100 h exposure to 1 h cycles at 1300 ☌ in a 90% H 2O-O 2 atmosphere. Even further improvement was achieved by adding a Si-bond layer between the mullite and the SiC, as shown in Figure 22(a). Replacing the YSZ topcoat with a BSAS layer delayed the onset of accelerated oxidation in water vapor-containing atmospheres by more than a factor of 2 ( Lee et al., 2003). The BSAS layer was also more resistant to cracking, presumably due to its low modulus, which enhances the compliance of the coating. This overlay topcoat, termed as BSAS, is a low-silica activity ceramic of composition (1 − x)BaO- xSrO-Al 2O 3-SiO 2 (0 ≤ x ≤ 1), designed to minimize the selective volatilization of silica.

To improve the crack resistance of the coating, a more crack-resistant overlay coating was developed by Lee et al.
